

- Use click plc as modbus server how to#
- Use click plc as modbus server full#
- Use click plc as modbus server code#
- Use click plc as modbus server Pc#
Thanks goes to these wonderful people ( emoji key): If you can include a Wireshark PCAP captue, that would be very helpful as well. I need help! I've tested this with an Automation Direct Click PLC, but I need people to test with additional types of PLCs and submit issues. To change this, set simpleAddressing to false Hello - Has anyone used an Automation Direct CLICK PLC as a Modbus client to communicate to the robot’s Modbus server I am trying to use the CLICK PLC’s receive/send instructions to read coils. Modbus Addressing: By default, register and coil addresses will be 0 indexed, not using Modbus addresses.
Use click plc as modbus server Pc#
About Master and Slave, think like internet: a website is the Master and your pc that browse the site is the Slave. Start a ModbusTCP server, and listen for all implemented Modbus commands. To use nModbus you need to add the Modbus libraries to the plc program.
Use click plc as modbus server full#
The error handling is consistent and easy, and it has a full test suite to ensure repeatable behavior. It's written in Typescript, so you get easy to use strong typings. The aim of this project is to make it extremely easy to work with Modbus with Node.js. You are now reading and writing data from LabVIEW to a PLC.Simple-modbus A simple library for working with Modbus And Voila! The random array of values we sent from the PLC has been transmitted successfully. In this example, the value 999 was written to address 0, and then all the holding register values were read and populated in the “register values” indicator. As always, make sure to close the connection when you are done. Then, you can write and read registers as you choose. You will need to create a TCP connection to the IP address of the PLC as well as use the same local port number (502) in your “serverData” data block. All VIs are taken from the Modbus Master.lvclass and are listed below.
Use click plc as modbus server code#
On the LabVIEW side, the code is straightforward. A Modbus client (LabVIEW) sends its messages on the port 502, and a Modbus server (PLC) receives messages on 502. 1.2 Function Block to Use The Modbus TCP Server. The function block eliminates the need for programming data exchange, making it easy to execute the Modbus TCP Server function. Local Port: This is the outgoing port number of the local connection partner (value range: 1 to 49151), 502 is the default. The Modbus TCP Server function automatically responds to access to the Work Area or Data Memory Area of the CP2E CPU Unit from a Modbus TCP client on the host PC or PLC.Remote Port: This is the incoming tunnel port number of the remote connection partner (value range: 1 to 49151) or 0 for any.For example, if the IP address of my computer is 192.168.0.73, the addresses will be. Remote Address: The default address is 0.0.0.0 (any IP address), but you can enter a specific IP address so that the server only responds to requests from this address.Active Established: Select false for passive connection establishment.Connection Type: 11 is for TCP connections.If you have multiple “MB_Server” blocks, they will each need unique numbers. ID: A unique ID for the connection within the CPU ranging from 1 to 4095.InterfaceID: This references hardware identifier number, found in “Devices and Networks”, pictured below.
Use click plc as modbus server how to#
Details on how to populate this are listed below. The data block should be of type TCON_IP_v4, which includes all address parameters required for establishing a connection. You will also need space in a data block to save configuration information to connect using Modbus.
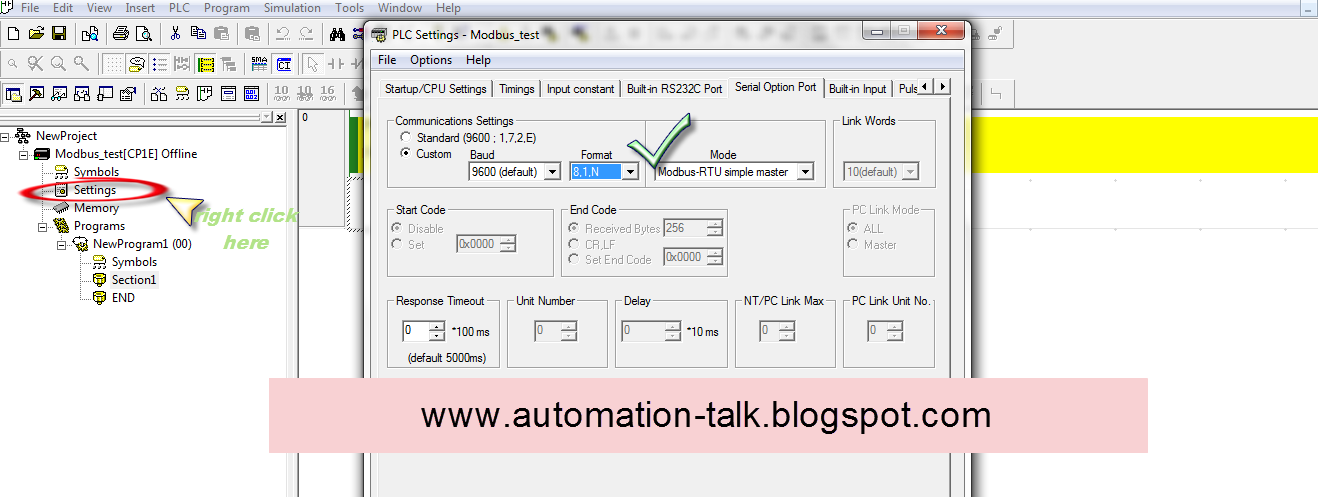
Mine is named “dbHoldingRegisters” and I filled it with an array of random values to send to LabVIEW. You will need to create a data block for holding registers, which contain the information you are trying to send and receive. This will be the only rung you need in Main. To set up Modbus Communication in TIA Portal, drag an “MB_Server” block to the Main. Modbus is an easy to deploy protocol that enables multiple devices on the same network to communicate. Hello - Has anyone used an Automation Direct CLICK PLC as a Modbus client to communicate to the robot’s Modbus server I am trying to use the CLICK PLC’s receive/send instructions to read coils. Modbus TCP is an excellent way to transfer data between the two programs. The list of different benefits these two offerings is long, but what if you need both? Have you ever needed to integrate LabVIEW into a Siemens PLC project or vice versa? PLCs offer features such as reliability and safety, whereas LabVIEW has plug and play libraries for a variety of hardware. Modbus TCP - GE PLC Conversions Genius M10 Modbus TCP.pdf Modbus TCP Overview - Modbus/TCP Serve The PACSystems products listed below support Modbus/TCP Server functionality: ⢠Deepsea Dse5310 Modbus on K40 aSENSE - Microsoft Modbus is a simple, open protocol for both PLC and sensors.
